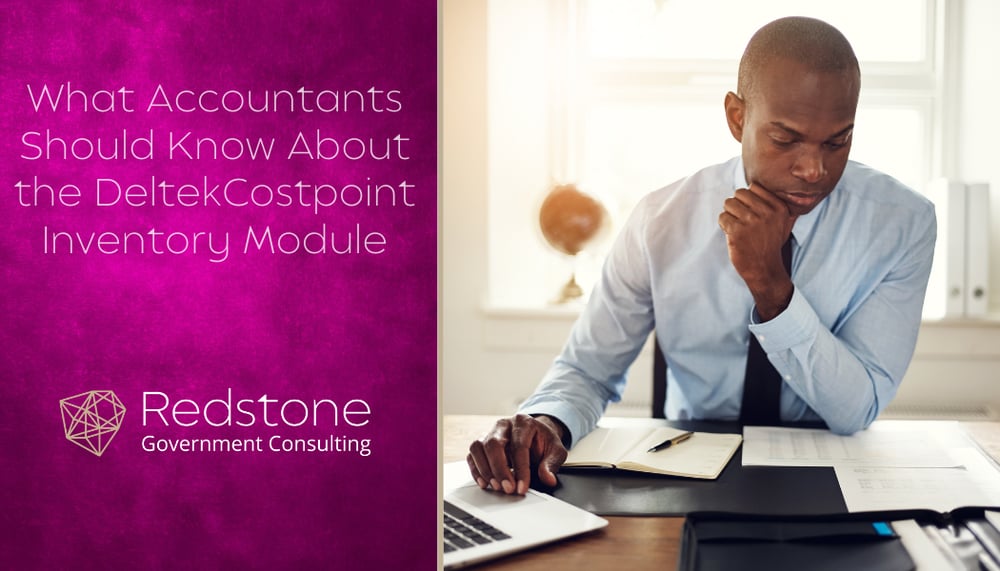
I find that depending on whether your job is on the Finance & Accounting (F&A) side or the Materials & Manufacturing side of the business, the perception of the capabilities and benefits of the Deltek Costpoint Inventory module tend to vary drastically.
In this article, we will clear up some of the common misconceptions of the inventory module that we tend to encounter when working with Finance & Accounting-minded people. We will also highlight some of the more powerful capabilities of the Costpoint Inventory module which extend far beyond just F&A’s needs, much of which you may not even realize are already at your fingertips. By setting everyone to the same level of understanding of full capabilities and helping them to see the “big picture” from all angles, your business can break down silos and operate your Costpoint Inventory Management system in the most effective manner, collectively yielding broad benefits for the entire organization.
In Costpoint, “Inventory” is Not Just “Current Assets”
One of the first things I often find when I use the word “Inventory” when speaking to an F&A minded person is an immediate tunnel vision on the Balance Sheet, more specifically the Inventory Account(s) on the balance sheet (i.e. Assets). The Inventory module in Costpoint provides far more than just the ability to track Asset inventory. Understanding this is critical to unlocking the full capabilities of the Inventory module and tends to be that “ah ha” moment for many.
Costpoint provides the capability to track 3 types of “stuff,” which in Costpoint we will refer to collectively as “Inventory,” not to be confused with the accounting view of the word “Inventory” meaning “Current Assets.” When we talk about tracking the “stuff” that we have, we are talking about the ability to look at a stock status report to see exactly what “stuff” (inventory) we have, where it is located, how much it is worth, any sorts of traceability/history on the item, and even historical records of what “stuff” we HAD and how it was consumed. In Costpoint this tracking of all types of “stuff” is handled by the Inventory Ledger (IL), which is separate from the General Ledger (GL).
When we talk about all the “stuff” we can track in the Costpoint Inventory module, we can break it into 3 distinct categories:
- Asset Inventory (which can be in the form of Raw or Finished Goods)
- Expensed Inventory
- Customer/Government Furnished Inventory
Category 1 tends to be the sole focus of the F&A minded, not realizing that even once “stuff” is expensed or furnished to the business, although in many cases we may no longer expect further impacts to the GL after the PO voucher, we still need to be able to track the material through its full lifecycle until final consumption. For an expensed item, the PO receipt and subsequent PO voucher may be the only financial transaction that really matters to accounting, but in the materials management world and the broader ERP system, that is only step one of that item’s journey through the Deltek Costpoint Inventory & Manufacturing modules.
To put it into perspective, if the Inventory module only housed “asset” items until their subsequent consumption (which in the “asset” world would typically be the moment at which they are expensed), but ignored unconsumed “expensed” and “furnished” items which are still sitting out on the shelves, how would a materials manager be able to look into Costpoint to see a full picture of what they had sitting on their shelves? Those other 2 categories of inventory are still physically available and unconsumed, even though they have already posted to the GL as an expense or as a nonimpact in the case of “furnished.” Many project-based GovCon businesses operate with zero asset inventory and solely operate in the expensed inventory world, since their customers are funding their manufacturing on direct projects, and they buy/manage their materials directly on those projects. To effectively plan and operate a manufacturing business, knowing what you have at all times, regardless of inventory category, is paramount to proper planning. Costpoint solves this problem by housing all 3 categories of “stuff” in one place, the Inventory module, and essentially tracks the 3 inventory categories in one common manner. Transactions performed in the Inventory module result in appropriate impacts (or non-impacts) to both the Inventory Ledger and General Ledger, depending on the type of inventory being transacted and your configuration.
You Don’t Need a Bunch of General Ledger Accounts to Track What Inventory You Have
I have found that businesses that don’t currently utilize the Costpoint Inventory module can sometimes have an overly complicated Chart of Accounts (COA) for their asset inventory, having many accounts housed in the same section of their Chart of Accounts in order to keep track of how much of varying types of products they have in stock. This is the result of not having a place to house all the necessary granularity of what all they have in stock and not wanting one GL asset account that just has a bulk amount of dollars in it without any further explanation of what makes up that cost. In those environments that don’t utilize the Costpoint Inventory module, the inventory data that would clarify the makeup of those GL dollars is typically housed in a spreadsheet or an external inventory management system that is managed outside of Costpoint by the inventory department. This causes lots of its own problems since it is very easy for the GL and the external inventory data to be out of sync with one another, since they are not interconnected.
This is where the Costpoint Inventory Ledger (IL) solves that problem for you. As will be further discussed below, the Inventory Ledger keeps track of all the important inventory attributes you would care about, thus you don’t need to create further granularity in your COA to track things that are otherwise standard in an Inventory Management System, nor do you need to maintain external inventory tools to track this data. The IL knows the Part, Rev, Owning Project/Account/Org, Cost, Quantity, and Location. It even is aware of things like whether the inventory is Expense/Asset/Furnished, and the Serial and/or Lot Number Traceability. Since the granularity is already tracked on the IL, you do not need to subdivide your COA on the GL to get costing of how much of any given item you have. All you need to do is run a stock status report within Costpoint and you will see and be able to filter/group/sort based on any and all of these attributes. No more needing to have 10 asset accounts for different part numbers, or a bunch of expense accounts based on what type of item it was. You can have a single “Raw Material” asset account, a single “Direct Materials” expense account, and so forth. The detail behind those accounts is what will be housed on the IL and full history can be reviewed there.
What is the Costpoint Inventory Ledger?
Understanding the Costpoint Inventor Ledger (IL) is the basis for understanding how Costpoint keeps track of your “stuff.” Every inventory transaction performed in Costpoint impacts the IL in real-time. The Inventor Ledger houses all the critical inventory information that you would be tracking (i.e. part, rev, cost, quantity, location, etc.). A snapshot of the Inventor Ledger at any given time is essentially what you see when you look at a stock status report, which is everything that you currently have at any given moment. The IL is a ledger though, keeping track of all historical transactions performed over all of time, allowing you to see a full inventory transaction history, even of parts no longer in stock.
The IL is what your receiving/materials management/inventory personnel are interacting with directly on a daily basis through the execution of Costpoint Inventory transactions (i.e. PO Receipt, Location Transfer, Project Transfer, Issue to MO, Issue to SO, Qty Adjustment, etc.). With few exceptions, these personnel don’t make decisions on whether their transaction has a financial impact to the GL or not. In their world, in a way, they don’t care. Costpoint, when properly configured, will handle all of the behind the scenes accounting to properly impact the GL where appropriate. Regardless of the impact to the GL, every transaction they perform will have an impact on the IL.
Think about it. I’d venture to guess that you don’t perform a Journal Entry (JE) when you want to record a PO cost to the General Ledger. Instead, you rely on the PO Voucher transaction that AP performs and that posts to the GL via the AP Subledger posting. A JE would be circumventing the proper process. The IL behaves in the same way. When you migrate to utilizing the Costpoint Inventory module, here’s the good news you’ve been waiting for - you will no longer need perform Journal Entries to move costs related to inventory transactions. Instead, your inventory team will perform their inventory transactions in the Inventory module and those transactions will naturally flow from the IL to the GL, as appropriate. Accounting is essentially removed from the day-to-day of financial inventory management…aren’t you excited?
This is where the type of inventory matters. Some inventory and transaction types are only tracked on the IL and do not touch the GL, while others may impact both. Much of this is decided based on your configuration, while others are decided based on the specific transaction or inventory type.
Some Examples of How Inventory Transactions Impact the Inventory Ledger vs. General Ledger
Expense-Based Inventory
For example, if we are talking project owned expense-based inventory, when I receive a PO Line that purchased 1 WIDGET @ $100, the Inventory Ledger increases in real-time to indicate I have 1 WIDGET @ $100. The GL still says $0 have been expensed, since it has not yet been impacted. The GL sees the $100 expense only once the PO voucher is posted.
Now let’s say that WIDGET sits on the shelf for a few months, the IL will show I have 1 WIDGET @ $100 in stock for that entire period of time, since it has not yet been consumed, even though the GL already reflects the $100 expense fully. When I consume that widget against the project or a Manufacturing Order (MO) on the project, in many cases I don’t want the GL to be impacted, since the expense already posted back when we vouchered the PO. I just want the stock status report to be reduced by qty 1 to say I no longer have that WIDGET in stock. The issue transaction will consume qty 1 @ $100 out of stock on the IL, and that will be reflected on my stock status report showing I now have zero of that WIDGET. In this case there would be no GL impact as a result of the material issuance, since the expense is already sitting at its final resting place.
Asset-Based Inventory
On the other hand, if this was asset-based inventory (i.e. common stock), the financial path would look different. The PO voucher would still be the initial touch point to the GL, but would reflect $100 in the asset account, which isn’t the final resting place of that cost since it will be consumed at some point in the future. When the subsequent issue transaction occurs, the IL will still be lowered in a similar fashion to above, but in this case that transaction would also impact the GL, posting a credit to the raw asset account and a debit to the direct expense account on the direct project that consumed the material.
Broadening Your Understanding of the Costpoint Inventory Capabilities
The Costpoint Inventory module offers far more than basic inventory tracking. It’s a powerful tool designed to support complex materials and manufacturing environments while ensuring compliance and control. Below are just a few of the advanced capabilities available to organizations looking to strengthen inventory management and integrate more fully with financial and operational processes:
- Real-time Inventory Visibility & Full Audit Trail, Directly Interconnected with the GL
- Min/Max Reorder Part Tracking & Automated PR Generation
- Borrow/Payback Project Transfer Capability – Fully FAR Compliant
- Warranty Tracking on both Vendor & Customer Warranties
- Inventory Labelling & Barcoding
- Shelf-Life Tracking/Automated Expiring Materials Reporting
- Physical & Cycle Counting
- Control to Prevent Improper Cross-Project Issuance
- Ability to Segregate Non-Conforming Inventory to Prevent Escapements
- MRP Planning/Full Visibility into Both Supply & Demand
- Government Property Tracking & FAR Compliant Reporting
This overview highlights just a portion of what the Costpoint Inventory module can do to support efficient and compliant operations. A deeper understanding of its functionality can uncover even greater opportunities to enhance planning, reporting, and control across your materials and manufacturing environment.
Supporting Smarter Inventory Management in GovCon
At Redstone Government Consulting, our team works closely with government contractors to implement, optimize, and fully leverage the Deltek Costpoint Inventory module. Whether you're looking to improve visibility across inventory types, streamline GL integration, or strengthen manufacturing operations, our experts provide the insight and hands-on support to align system capabilities with your business needs. Our approach also supports compliance with government contracting requirements, including Material Management and Accounting System (MMAS) standards. From configuration and training to ongoing consulting, we’re here to help you make the most of your Deltek Costpoint investment.